Visual AIM
Visual Asset Integrity Management
Visual AIM offers more than risk based analysis. The system optimizes the mechanical integrity and reliability of any group of assets using comprehensive Risk Based Analysis (RBA), internal corrosion data management and inspection data management tools.
Asset integrity management is critical to the operation of any process facility. That’s why it’s important to closely monitor and manage the health and remaining life of fixed equipment. Failure to do so may expose your operation to equipment failure, unplanned downtime, loss of containment and even loss of life. The resulting financial consequences can be dramatic, including repairs, scrapped inventory, lost production output and severe environmental and regulatory fines.
The VisualAIM technology sets the standard for corrosion monitoring and predictive inspection scheduling. This powerful tool enables operators to input, organize, analyze and document thickness inspection data.
Software Overview
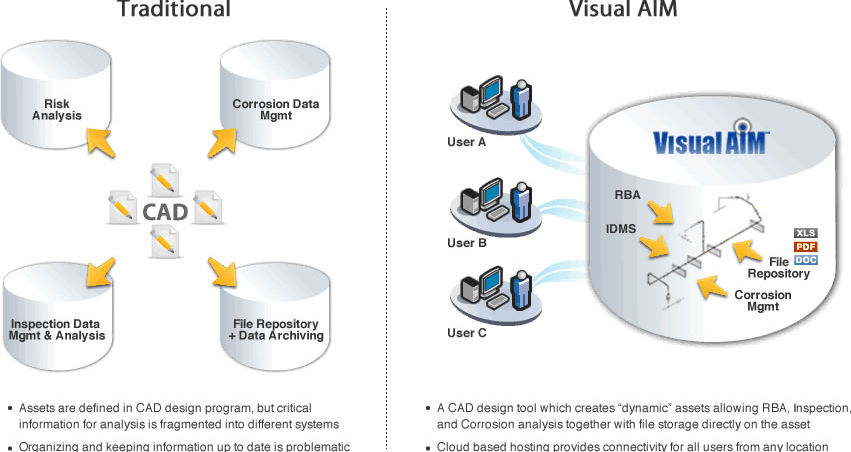
- Inspection Data Management System:
If the data and reports are not available then the inspections did not occur. This module provides a repository for ultrasonic thickness gauging, visual inspection, digital x-ray images, advanced inspection data reports, and much more. Corrosion Rates, Remaining Life, Maximum Allowable Operating Pressures, Retirement Dates, plus more are calculated and used to determine re-inspection intervals.
- Smart-Isometric Drawing Module:
An on-line isometric drawing system enabling users to quickly draw and store isometric drawings within the inspection database. Inspection data is populated on drawings if the user determines necessary. As drawings change, updates to the isometrics are performed quickly. Since the drawings are tightly integrated within the database users can see how and when changes occurred by using the built-in tracking and trending features.
- Corrosion Data Management System:
Mechanical integrity involves much more than visually inspecting and recording ultrasonic thickness readings. Internal corrosion coupons, corrosion inhibitors, fluid laboratory testing, and pipe to soil potentials must also be monitored and managed. The system provides the user a single location to enter data and report data trends. Since many operators contract various vendors to perform data collection the system incorporates a separate user security setting so multiple contractors can enter data across the entire company infrastructure. Risk Analysis Module: Performing inspections and thickness gauging is one of many variables to manage when creating inspection and maintenance budgets. Risk based analysis within the mechanical integrity world is used to identify damage mechanisms, select appropriate inspection and testing techniques, and evaluate overall risk from a financial, safety and environmental perspective. In addition the Visual AIM results are used to project future inspection, testing, maintenance and preventative maintenance strategies. The Visual AIM system incorporates the American Petroleum Institute (API) 580 and (API) 581 standards.
- Data Archiving Module:
Oil and Gas operators have a tendency to lose critical data associated with processing equipment. The drawings, inspection reports, and radiographs are stored in files located throughout a facility. The Data Archiving System within Visual AIM enables the user to simply upload to the database any digital data records which may be associated with a particular piece of equipment. The on-line systems records can be viewed, downloaded, and uploaded by users with appropriate security settings.
- On-Demand / Cloud Hosting:
The Visual AIM software is a hosted SaaS product accessible through the Internet or your secure intranet which means you can manage any facility from any location throughout the world. Visual AIM cloud computing facilitates easy collaboration between individuals in many different locations throughout the world. As upgrades, bug fixes, or customizations are added to the software, these new features are pushed out to users automatically. There is no need to constantly confirm the most up-to-date version is installed.
Key Features
-
Web based interface accessible from any computer
-
No software training needed, just log in and go
-
Multiple user levels from data entry to full administration
-
No complicated setup or steep learning curve
-
Create a system in minutes, not days or weeks
-
Risk analysis summary of all assets in one-click
-
Visual interface with a rich graphical display
-
Drag/drop interface for Intuitive workflow
-
Real-time collaboration and data feeds
-
Real-time calculations for risk analysis data
-
Customizable reporting available quickly
-
All data is stored in a secure SQL database format
-
Data is accessible via secure password protection and encryption
-
Inspection Data, Corrosion Data and Document Management
-
Historical trending viewed through statistical charting
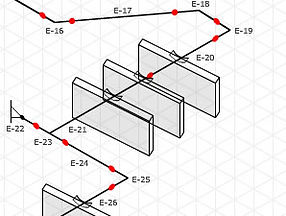
Technical Features
-
Applicable to upstream, midstream, refining, petrochemical
-
Process changes are easily and quickly updatedInternet/Intranet SaaS (Software as a Service) allowing for data collaboration
-
Stores data, inspections, schematics, reports, photographsMultiple theoretical and actual corrosion rate calculations
-
Calculates risk and risk rankings according to API RP 581>Customizable risk matrix per customer requirements
-
Visual representation of risk via color-coded icon display
-
Chemical management through follow up of technical variables & consumption rates
-
Ability to review and perform trending on monitoring system results
Full Process Standards
UPSTREAM
-
Incorporates oil and gas production specific failure mechanisms
-
Determines corrosion rates using DeWaard & Williams modified correlation
-
Determines errosional using API RP14E and The University of Tulsa model
-
Evaluates the risks for Cathodic Protection Systems and stores all associated data
-
Calculations utilize indstury standard: API 580, API 1160, ASME B31.3, ASME VIII Div 1
-
Determines internal corrosion velocities in static equipment, gathering lines & piping
MIDSTREAM
-
Determines internal and external corrosion velocities in pipelines and static equipment
-
Incorporates compressor stations, pump stations, associated liquid storage facilities
-
Calculations in accordance with standards: ASME B31.4, ASME B31.8 & ASME B31.8
DOWNSTREAM (PROCESS PLANTS)
-
Uses ASME B31.3, ASME VIII Div 1, API RP 580 and API BRD 581 industry standards
-
Sophisticated rule based analysis is also employed to rank the probability of failure
-
Expert Modes of Failure and Damage Mechanisms based on API RP 571
Inspection Module
-
Incorporates oil and gas production specific failure mechanisms
-
Determines corrosion rates using DeWaard & Williams modified correlation
-
Determines errosional using API RP14E and The University of Tulsa model
-
Evaluates the risks for Cathodic Protection Systems and stores all associated data
-
Calculations utilize indstury standard: API 580, API 1160, ASME B31.3, ASME VIII Div 1
-
Determines internal corrosion velocities in static equipment, gathering lines & piping